DBL 7381
What suppliers should know
What changes does the new corrosion test according to DBL 7381 (edition 2021-01) bring?
The introduction of the new corrosion cyclic test in accordance with DIN 55635 (VDA 233-102 / "VDA new") has been completed in DBL 7381 and Mercedes-Benz (formerly Daimler) is thus aiming to replace the previous test procedure in the medium term. In the initial sample process (PPAP), the previous corrosion change test represents one of the longest test cycles with a test time of ten weeks.
Significant changes
- Reduction of the testing time by 40 percent
- 4 weeks time saving compared to the "old" corrosion cyclic test according to DBL 7381
- Technologically advanced
- Testing performance is only permitted in programmable "combination chamber" ("MBN 10494-6")
Areas of application
The DBL 7381 (2021-01) specifies the corrosion change test 2 for the following cases:
- Materials/basic materials: steel, galvanised steel and aluminium
- Coatings: e.g. KTL, single/multi-layer coatings, powder coatings, baked multi-layer coatings.
- AA 10, 11, 12: Components in the engine compartment/underbody with medium corrosion load (differentiation from AA 20 + 22 KTL coated and AA 40)
- AA 20, 22: Components with cathodic dip coating on underbody/body parts etc. with particularly severe corrosion load
- AA 30: Decorative/functional parts e.g. Parktronic sensors, bezels etc.
- AA 31: Body parts e.g. boot lid, bonnet etc.
DO YOU HAVE FURTHER QUESTIONS?
TEST CHAMBER FOR DIN 55635
Technical features
test room
180 cm x 80 cm x 80 cm
range of temperature
-20°C to +60°C
relative humidity
30 % - 95 %
floor load up to
300 kg
Overview test methods
- DIN EN ISO 9227 (NSS)
- DIN EN ISO 11997-1 Cycle B
- VDA 621-415
- PV 1210 (Volkswagen AG, VW and Audi)
- DIN EN 60062-2-52 S1
- DIN EN 60062-2-52 S2
- DIN EN 60062-2-52 S3
- Volvo STD 423-0014 (complete)
- DIN 55635 Zyklus ABC (complete)
- DIN EN ISO 6270 CH
- DIN EN ISO 6270 AHT
- Ford CETP 00.00 – L – 467
Customer feedback
"I like your coordination team
because of your dynamism and trustworthiness."

“Thank you very much for your response and
for your focus on understanding and satisfying customer needs”

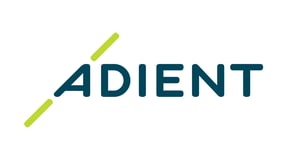
"Thank you very much
for your constant support and prompt reply."
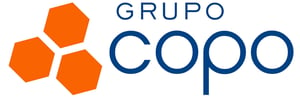
“You have always been a great help.
It has been an absolute delight to work with you”
